Powder coating mirror cabinets are an enduring classic piece of furniture, often employed to store items, organize decorations and serve as both functional and decorative features in both residential and commercial environments.
1. Appearance of Powder Coat Mirror Cabinet
1.1 The Rising Popularity of Industrial Style
Iron materials used in furniture production have long been associated with industrial-style furniture production. This aesthetic emphasizes simplicity, firmness and practicality–elements which iron materials exemplify perfectly.
1.2 Advances in Material Technology
The development of the iron dusting mirror cabinet has closely paralleled advances in dusting technology. Powder spraying technology enables iron surfaces to have greater durability, corrosion resistance and aesthetic value, opening up more opportunities for furniture production from iron materials.
1.3 Needs of Modern Life
As life evolves, people’s needs for furniture also shift. Iron powder mirror cabinets combine modern simplicity with practical functionality, satisfying people’s demands for beauty and practicality in furniture.
1.4 Raised Awareness of Environmental Protection
Iron material and powder coating usually found in iron spray mirror cabinets are environmentally friendly materials, satisfying modern society’s environmental protection and sustainable development requirements and having been received positively as such by society at large. As such, they have received some preference from society as a result.
2. Structure and Material
2.1 Ferrous Material
Powder Coating Mirror Cabinet is generally constructed from iron material for durability and stability, which makes the structure long-term reliable and long-lived.
2.2 Dusting Coating
Surfaces may be coated with powder coating for anti-fade and wear protection and corrosion resistance. This treatment has the added advantage of not fading over time. Having explored the robust structure and materials used in constructing powder-coated mirror cabinets, we now turn to their innovative design features that not only enhance functionality but also complement modern interiors.
Powder coating is the preferred finishing process for iron powder cabinets due to its durability, versatility, and environmental benefits. Typically, the powder used is a thermosetting polymer powder, such as epoxy, polyester, or a hybrid blend.
The process involves several steps:
① Preparation: The metal surface of the cabinet is cleaned to remove any contaminants like oil, grease, or rust. This ensures proper adhesion of the powder coating.
② Powder Application: The powder is electrostatically charged and sprayed onto the surface of the cabinet, which is grounded. This creates a strong attraction between the powder particles and the metal surface, ensuring even coverage.
③ Curing: The coated cabinet is then heated in an oven to allow the powder to melt and form a continuous film. This curing process chemically cross-links the polymer molecules, creating a durable and resilient finish.
④ Cooling and Inspection: After curing, the cabinet is cooled to room temperature and inspected for any imperfections or defects.
2.3 Powder Coating Advantages for Iron Cabinets
Powder coating offers significant advantages for iron cabinets, particularly in terms of moisture resistance and corrosion protection. The thick and uniform coating acts as a barrier against moisture, preventing it from reaching the underlying metal substrate. This inhibits rust formation and extends the lifespan of the cabinet, making it suitable for environments prone to humidity or moisture exposure.
Additionally, powder coating is inherently resistant to corrosion, offering superior protection compared to traditional liquid coatings. This is especially beneficial for iron cabinets used in outdoor or high-humidity environments, where exposure to moisture and corrosive elements is common.
Industry studies and case research consistently highlight the benefits of powder coating for iron cabinets. For instance, a study by the Powder Coating Institute found that powder coating surfaces exhibited greater resistance to corrosion, chipping, and fading compared to liquid coatings. This makes them ideal for long-term durability and aesthetics in various applications. Similarly, case studies from manufacturing facilities demonstrate cost savings and environmental advantages associated with powder coating. It includes reduced material waste, energy consumption, and VOC emissions, further underscoring its suitability for iron cabinet finishing.
3. Design Feature
3.1 Mirror Design
Powder coating mirror cabinets often include mirrors on their doors and cabinet bodies to enhance space perception while making any indoor area appear brighter and larger.
3.2 Multifunctional Storage
Powder coating mirror cabinets are typically designed with storage in mind, featuring various compartments or drawers that can help organize and store various items.
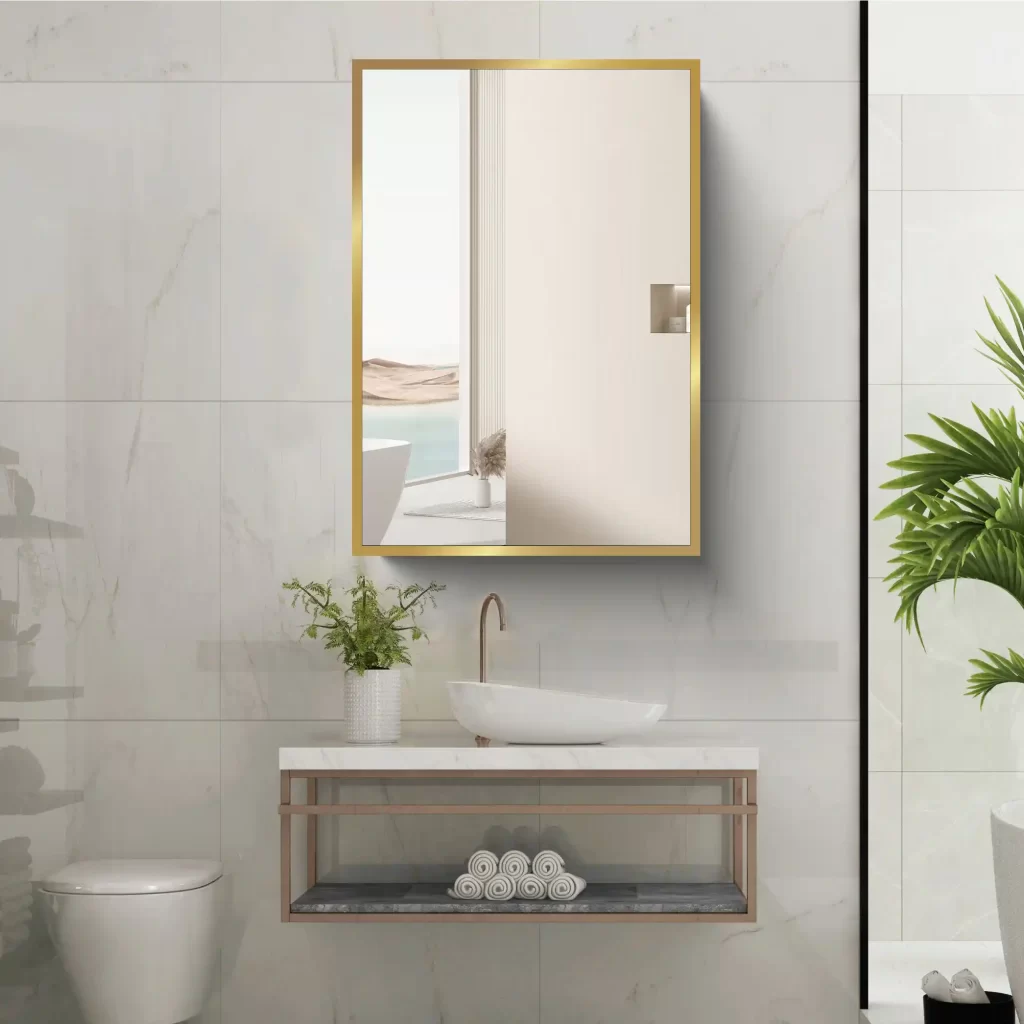
4. Uses and Scenarios
4.1 Living Room Decoration
The powder coating mirror cabinet can serve both decoratively and for storage in living room decor settings. It offers space to place decorations or household items while acting both decoratively and storing-wise.
4.2 Bathroom Storage
Bathroom storage typically involves organizing a variety of items such as toiletries, towels, and cosmetics to keep them accessible and easy to sort. A powder coating mirror cabinet, designed with multiple compartments and drawers, offers substantial storage space, facilitating organized and accessible storage for various items. Furthermore, powder coating mirror cabinets often come equipped with makeup mirrors that provide ample lighting and reflection functions to assist people with daily care processes such as makeup application, face washing and teeth brushing – providing convenient lighting functions and reflection functions so people can complete daily care procedures more easily and complete daily care tasks and finishes more effectively and quickly than before.
4.3 Moisture-proof Function
Most powder coating mirror cabinets possess some level of moisture resistance to protect them against humidity in the bathroom environment and avoid moisture-related issues that could otherwise compromise their service life and appearance. This protects the cabinet from moisture damage, extends its service life and keeps its appearance looking brand new for longer.
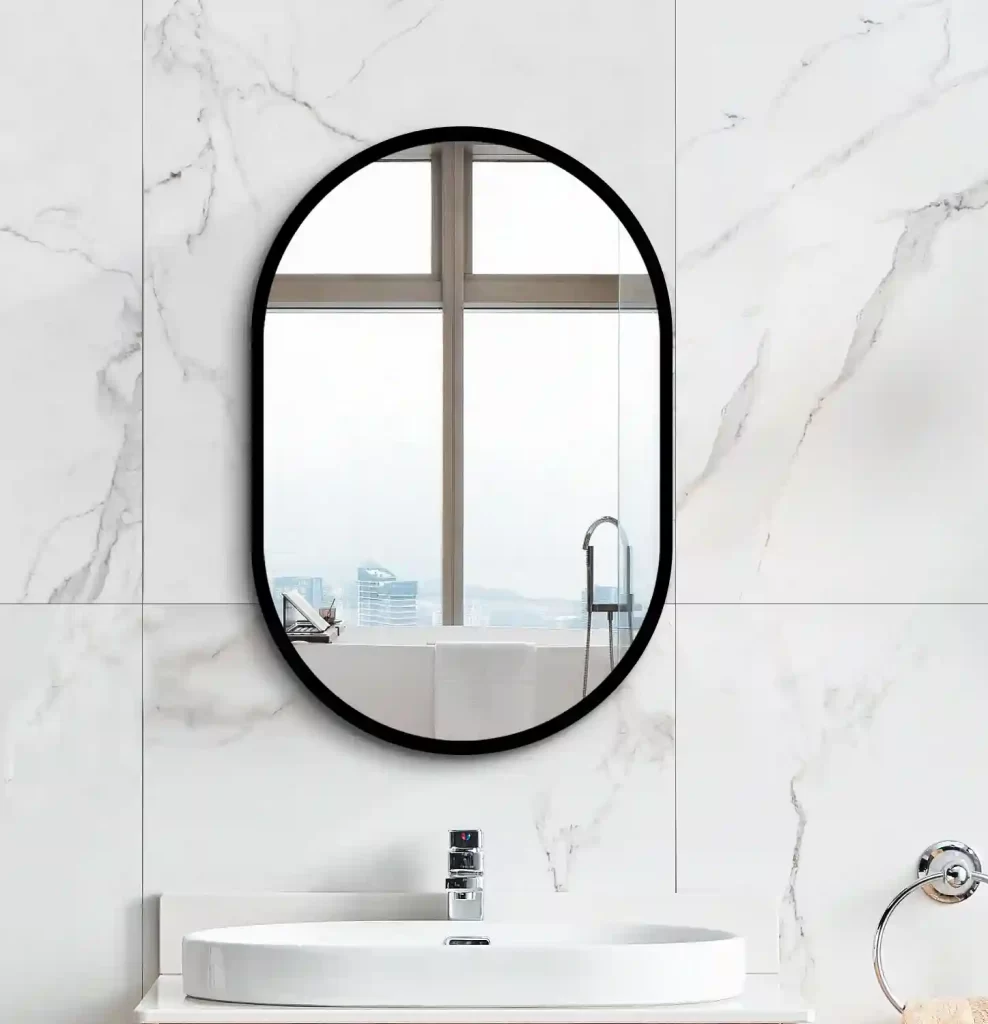
Here is a table based on the current market for powder coating mirror cabinets. This table provides an overview of the usage of powder coating mirror cabinets in different countries/regions:
Country | Percentage of Usage (%) |
United States | 35 |
China | 25 |
Germany | 15 |
Japan | 10 |
United Kingdom | 8 |
France | 5 |
Canada | 4 |
Australia | 3 |
South Korea | 3 |
Others | 2 |
5. Product Process
5.1 Stores Reserve
Before production can commence, all necessary materials need to be assembled; these primarily include iron materials, mirror materials and powder coating materials which must meet design requirements as well as quality standards.
5.2 Cutting and Machining
Iron is cut and machined into desired shapes and sizes according to design drawings, using mechanical or CNC equipment to ensure maximum precision and efficiency.
5.3 Welding and Assembly
This phase necessitates sophisticated operational techniques and high-quality welding processes for assembling the main structure of the powder coating mirror cabinet. This step ensures the stability and safety of the powder coating mirror cabinets.
5.4 Powder Coating
Once assembled, the mirror cabinet is uniformly coated with powder to enhance its appearance while providing corrosion and wear protection. Powder coating increases product beauty while offering corrosion and wear resistance features.
5.5 Mirror Mounting
After cutting and milling, mirror material is installed into its position on an iron powder spray mirror cabinet. In order to ensure the uniformity and perfection of the installation process, precise installation must be carried out during this process.
5.6 Quality Inspection
Upon completion of production, the powder-coated mirror cabinets are subjected to stringent quality control inspections, including appearance inspection, size verification and structural stability testing. Only those products that pass these rigorous quality checks may be sold from the factory.
5.7 Packing and Shipping
After packing and shipping are complete, the qualified iron powder mirror cabinet can be transported directly to either its sales point or the location specified by its customer. Proper packaging protects products from being damaged in transit while making handling more manageable.
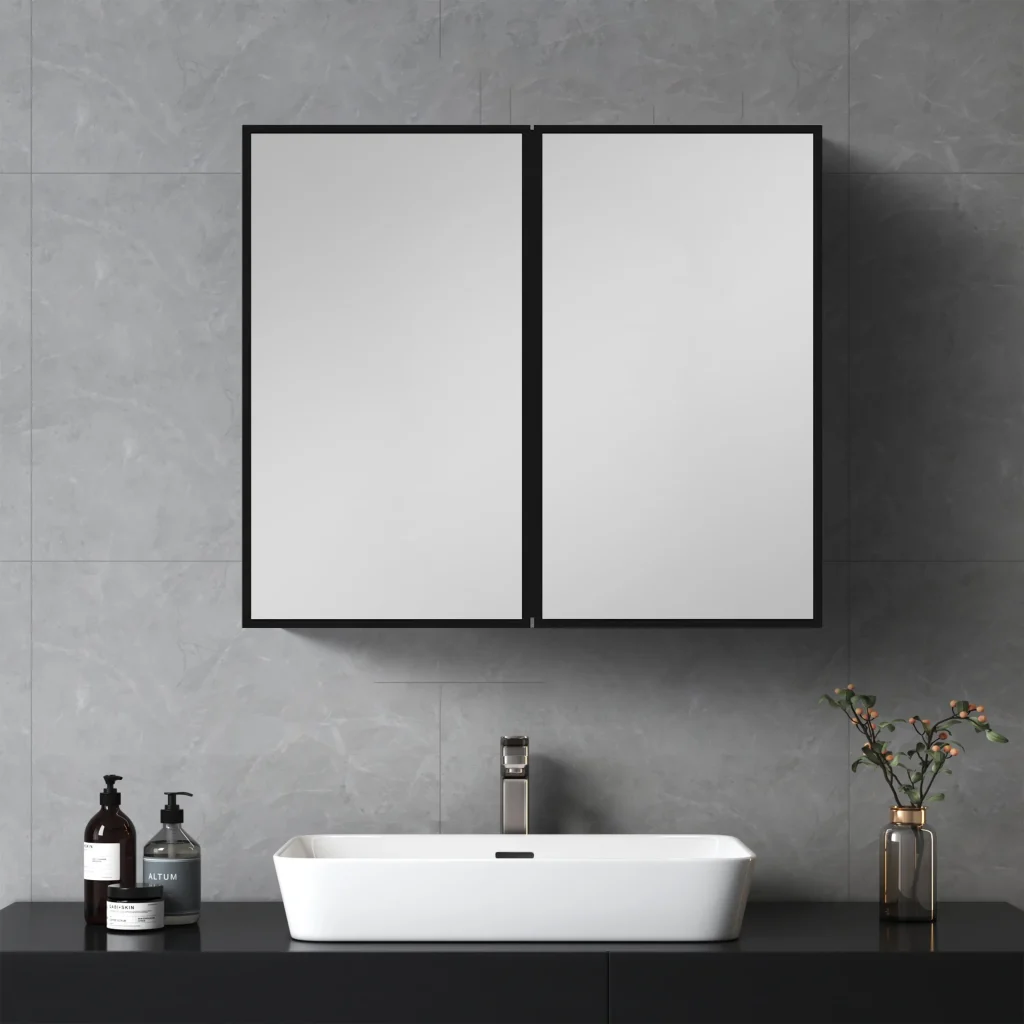
6. Maintenance and Precautions
6.1 Regular Cleaning
Use a soft damp cloth or sponge to wipe the surface of the powder coating mirror cabinet gently to remove dust and dirt. To avoid damaging its dusting coating use only cleaners without acidic or alkaline ingredients as these may damage it further.
6.2 Anti-scratch
Avoid using sharp or hard objects to directly scratch the surface of the iron spray mirror cabinet, so as not to scratch or wear the surface.
6.3 Avoid Moisture and Damp Environments
Iron powder mirror cabinets must be stored in dry and ventilated conditions in order to prevent long-term exposure to moisture or humid environments that could damage their iron powder layers, which could result in corrosion or other forms of damage.
6.4 Regular Checking
Regular checks should be conducted on the iron spray mirror cabinet to ensure its stability and safety, and any loose or damaged parts should be repaired in time.
6.5 Use Soft Cushions
When placing items on an iron dusting mirror cabinet, use soft cushions (rubber cushions) to reduce direct contact between the item and the surface and to reduce scratching or other forms of damage to both.
6.6 Apply Wax or Conditioner Regularly
Regular application of wax or conditioner to iron furniture provides protection and care, prolonging its service life and increasing luster.
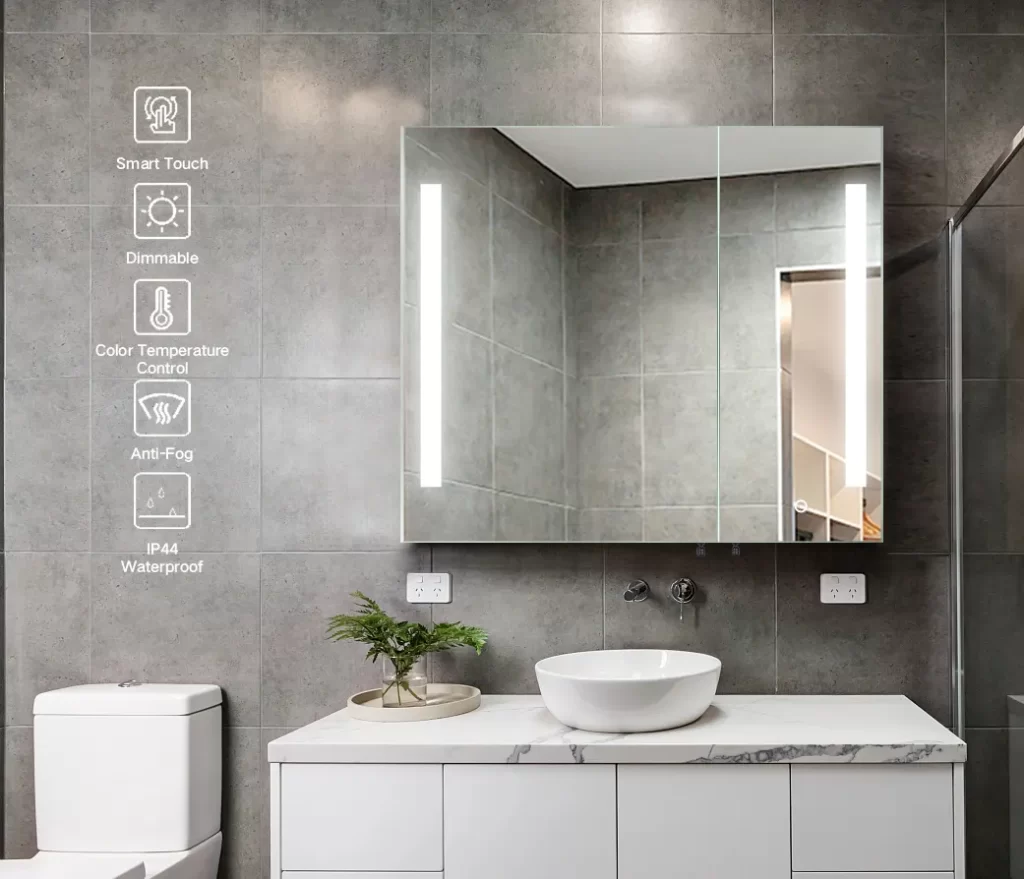
7. Rust Prevention Test
7.1 Prepare Test Equipment
The salt spray chamber or salt spray room, capable of simulating an actual salt spray environment, must be prepared. Furthermore, any additional tools or equipment as detailed by test standards must also be available and ready.
7.2 Prepare a Sample
Collect multiple iron spray mirror cabinets samples of differing batches or specifications of products for accurate testing purposes. Be sure that no coatings or coverings exist on their surfaces to ensure accurate test results.
7.3 Set Test Conditions
Set test conditions by test standards or requirements by setting parameters such as temperature, humidity and brine concentration in a salt spray test chamber. Typical settings for salt spray testing typically include normal temperatures; relative humidity between 95%-96% and salt concentration of between 5%-10% in salt water concentration.
7.4 Testing
To conduct the salt spray testing of your iron spray mirror cabinet sample, set the salt spray test chamber’s timer according to your requirements and begin. Testing times typically range from several hours up to hundreds of hours or even thousands.
7.5 Observe and Record
Testing involves closely observing and documenting the surface conditions of samples to detect corrosion, oxidation or other surface changes that require attention. At regular intervals, observations and records will be made of any pertinent observations or changes noted during observation or testing.
7.6 End Output
Once testing has ended, the sample is removed, cleaned and checked for surface conditions before being evaluated according to test results for corrosion resistance evaluation and product/production process improvement.
7.7 Analyze Data and Reports
Conduct data analysis and summarize test results; compile test report with conditions, observations results, conclusions and suggestions for improvement.

8. Wall mounting of Mirror Cabinet
8.1 Select Installation Location
To choose an installation location for the mirror cabinet, consider both functionality and aesthetics when making this selection. Make sure there are no concealed cables or pipes above its desired location, and ensure it can be reached easily for use.
8.2 Prepare Installation Tools and Materials
Before installation, gather the tools and materials required, such as electric drills, screwdrivers, measuring tools, screws, wall nails and wall plugs as per product manual specifications. Ensure all tools are complete as per installation manual recommendations.
8.3 Measurement and Marking
Utilize a measuring tool to take accurate measurements of dimensions and horizontal lines at your installation location, then mark its center point and boundary line on the wall for later drilling and installation.
8.4 Drilling and Installing Wall Hangings
After marking their desired locations on the walls with painter’s tape, drill holes using an electric drill by these markings. Install the hangings using screws as appropriate ensuring their proper positioning in terms of accuracy, horizontality, and security.
8.5 Mounting Mirror Cabinet
When mounting mirror cabinets on walls, first align their backplane or fixing bracket with the pendant attached to the wall pendant and hang them according to the manufacturer’s instructions ensuring secure placement vertically and horizontally. Use screws or other fastening methods as required to secure them to the wall for secure attachment of your cabinet to its supporting structure.
8.6 Adjusting and Fixing
Once installed, take time to carefully and correctly align and secure the mirror cabinet to ensure proper positioning and stability. If any necessary adjustments need to be made to its position or levelness, loosen its fixing screws, adjust as necessary and refix.
8.7 Clean and Tidy
Once installation is complete, take time to ensure a tidy environment by clearing away debris from the installation area and placing items inside a mirror cabinet as part of the final steps of this process.
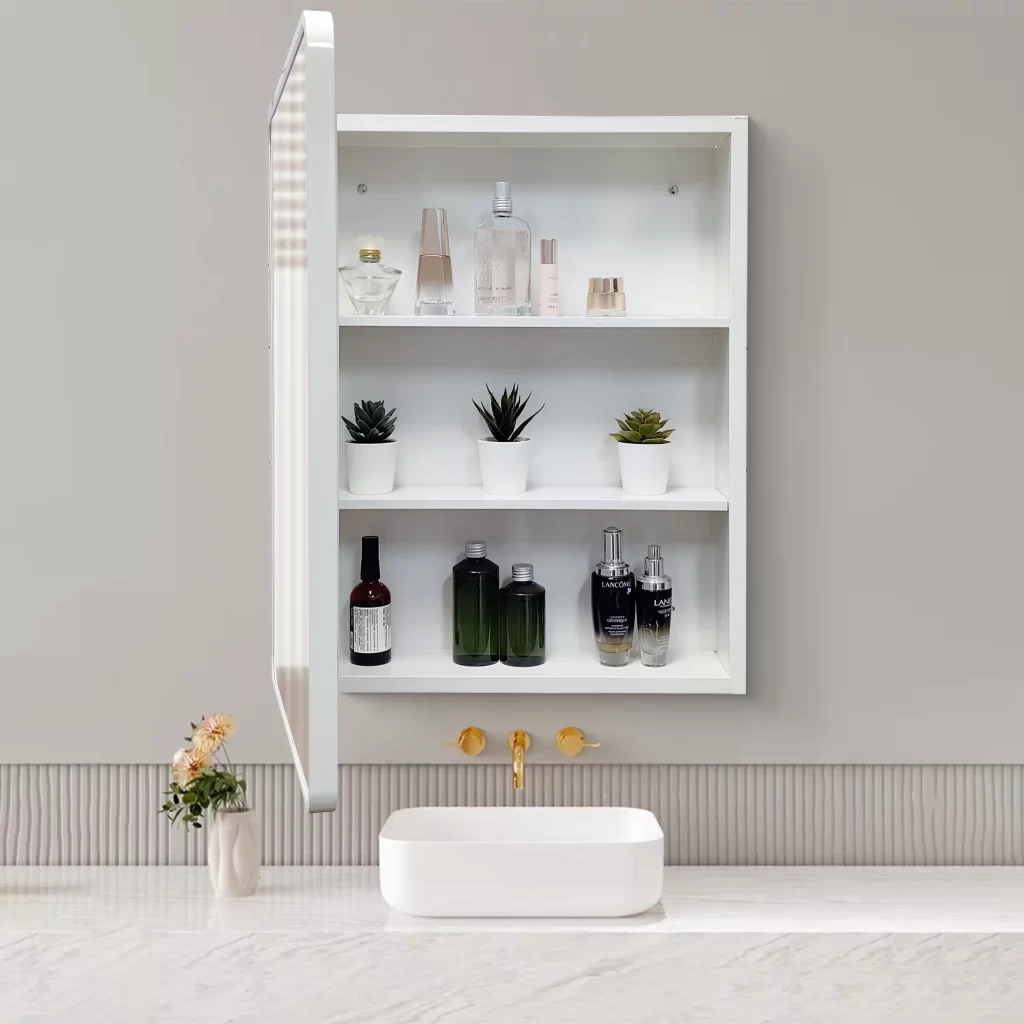
9. Packaging and Transportation of Powder Coating Mirror Cabinet
Our packaging team takes great care in packing our factory products so they arrive clean and undamaged, while anti-fall packaging helps ensure their safety during transportation.
9.1 Cleaning Product
To clean our product, a jet gun is first used to blast away dust or other impurities residing on its surface with air. After this step has been taken, gloves are worn before using alcohol-soaked wipes on both its mirror surface and cabinet body to eliminate stains on mirror cabinet bodies and make our product sparklingly clean.
9.2 Protect the Surface of the Mirror
After cleaning, a protective film will be attached to the surface of the mirror to avoid impurities and scratching of its surface.
9.3 Preparation of Packaging Materials
We typically utilize foam, pearl cotton and honeycomb board as our packaging materials, tailoring each one according to customer needs and ensuring sufficient protection and ease in handling/security for their product.
9.4 Marks and Labels
Mark the product with its name, model number, quantity and other pertinent details to facilitate easy identification and management. Fragile or light products should be marked accordingly with an additional warning label attached.
9.5 Check the Quality of Packing
Once the packaging process is completed, its quality must be carefully examined to ensure there are no leaks, damage or looseness in its design.
9.6 Transport
Based on the size and weight of our product, we select an appropriate method of transportation with transport packaging for safety. Once packed into an iron powder spray mirror cabinet box, place it within an automobile or container for transport for safe arrival at our location.
FAQ
1.What materials are typically used in the construction of powder coating mirror cabinets?
Powder coating mirror cabinets are generally constructed from iron materials for durability and stability. Additionally, surfaces may be coated with powder coating for anti-fade, wear protection, and corrosion resistance.
2.How should I maintain and care for a powder coating mirror cabinet?
Regular cleaning with a soft damp cloth or sponge is recommended to remove dust and dirt. Avoid using sharp or hard objects to prevent scratches, and store the cabinet in dry and ventilated conditions to prevent moisture damage.
3.What are some common uses and functionalities of powder coating mirror cabinets in different countries?
Powder coating mirror cabinets are commonly used for storage and decoration purposes in various countries, with the United States, China, Germany, and Japan being the top users. They serve as functional storage solutions while enhancing the aesthetic appeal of living spaces.
4.How to find a professional custom Powder Coating Mirror Cabinet team?